Yüksek Gerilim Konnektörüne Genel Bakış
Yüksek gerilim konnektörleri olarak da bilinen yüksek gerilim konnektörleri, bir tür otomotiv konnektörüdür. Genellikle 60 V'un üzerinde çalışma voltajına sahip konnektörleri ifade eder ve esas olarak büyük akımların iletilmesinden sorumludurlar.
Yüksek gerilim konnektörleri, çoğunlukla elektrikli araçların yüksek gerilim ve yüksek akım devrelerinde kullanılır. Akü grubunun enerjisini farklı elektrik devreleri aracılığıyla akü grupları, motor kontrolörleri ve DCDC dönüştürücüler gibi araç sistemindeki çeşitli bileşenlere iletmek için kablolarla çalışırlar. Dönüştürücüler ve şarj cihazları gibi yüksek gerilim bileşenleri de bu bağlantı elemanlarıyla birlikte kullanılır.
Şu anda, yüksek gerilim konnektörleri için üç ana standart sistem bulunmaktadır: LV standart fişli, USCAR standart fişli ve Japon standart fişli. Bu üç fişli sistem arasında, LV şu anda iç pazarda en geniş dolaşıma ve en eksiksiz proses standartlarına sahiptir.
Yüksek gerilim konnektör montaj süreci diyagramı
Yüksek gerilim konnektörünün temel yapısı
Yüksek gerilim konnektörleri esas olarak kontaktörler, yalıtkanlar, plastik gövdeler ve aksesuarlar olmak üzere dört temel yapıdan oluşur.
(1) Kontaklar: Elektrik bağlantılarını tamamlayan çekirdek parçalar, yani erkek ve dişi terminaller, kamışlar, vb.;
(2) Yalıtkan: kontakları destekler ve kontaklar arasındaki yalıtımı sağlar, yani iç plastik kabuk;
(3) Plastik kabuk: Konnektörün kabuğu, konektörün hizalanmasını sağlar ve tüm konektörü, yani dış plastik kabuğu korur;
(4) Aksesuarlar: Konumlandırma pimleri, kılavuz pimleri, bağlantı halkaları, sızdırmazlık halkaları, döner kollar, kilitleme yapıları vb. gibi yapısal aksesuarlar ve montaj aksesuarları dahildir.
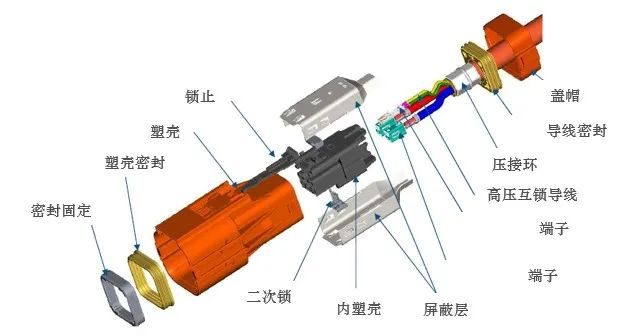
Yüksek gerilim konnektörünün patlatılmış görünümü
Yüksek gerilim konnektörlerinin sınıflandırılması
Yüksek gerilim konnektörleri çeşitli şekillerde ayırt edilebilir. Konnektörün koruma fonksiyonu olup olmadığı, konnektör pin sayısı vb. gibi faktörler, konnektör sınıflandırmasını tanımlamak için kullanılabilir.
1.Kalkanlama olup olmadığı
Yüksek gerilim konnektörleri, ekranlama fonksiyonuna sahip olup olmamasına göre ekransız konnektörler ve ekranlı konnektörler olarak ikiye ayrılır.
Ekransız konnektörler nispeten basit bir yapıya, ekranlama işlevine sahip olmayan ve nispeten düşük maliyetlidir. Şarj devreleri, pil takımı iç kısımları ve kontrol üniteleri gibi metal kasalarla kaplı elektrikli cihazlar gibi ekranlama gerektirmeyen yerlerde kullanılır.
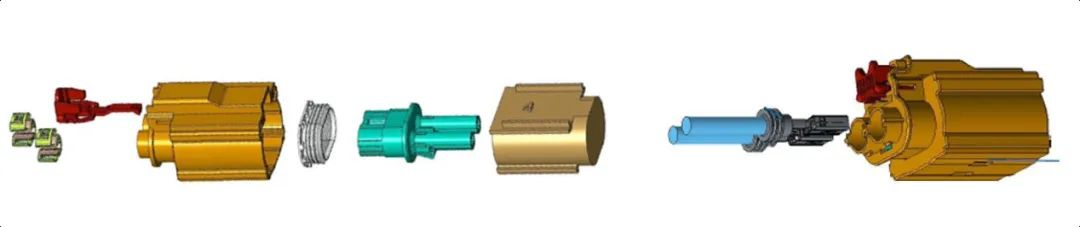
Koruma katmanı ve yüksek voltaj kilitleme tasarımı olmayan konnektör örnekleri
Ekranlı konnektörler karmaşık yapılara, ekranlama gereksinimlerine ve nispeten yüksek maliyetlere sahiptir. Elektrikli cihazların dış yüzeyinin yüksek voltajlı kablo demetlerine bağlandığı yerler gibi ekranlama işlevinin gerekli olduğu yerler için uygundur.
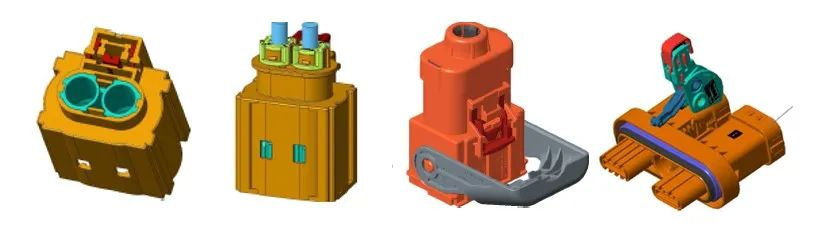
Kalkanlı ve HVIL tasarımlı konnektör Örneği
2. Fiş sayısı
Yüksek gerilim konnektörleri, bağlantı noktası (PIN) sayısına göre sınıflandırılır. Günümüzde en yaygın kullanılanlar 1P konnektör, 2P konnektör ve 3P konnektördür.
1P konnektör nispeten basit bir yapıya ve düşük maliyete sahiptir. Yüksek gerilim sistemlerinin koruma ve su geçirmezlik gereksinimlerini karşılar, ancak montaj süreci biraz karmaşıktır ve yeniden işleme kolaylığı düşüktür. Genellikle pil takımlarında ve motorlarda kullanılır.
2P ve 3P konnektörler karmaşık yapılara ve nispeten yüksek maliyetlere sahiptir. Yüksek gerilim sistemlerinin koruma ve su geçirmezlik gereksinimlerini karşılar ve iyi bakım kolaylığına sahiptir. Genellikle yüksek gerilimli akü grupları, kontrol terminalleri, şarj cihazı DC çıkış terminalleri vb. gibi DC giriş ve çıkışlarında kullanılır.
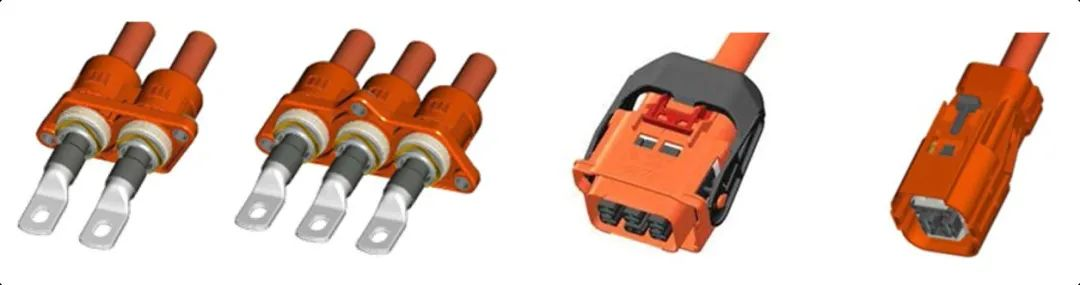
1P/2P/3P yüksek gerilim konnektörü örneği
Yüksek gerilim konnektörleri için genel gereksinimler
Yüksek gerilim konnektörleri SAE J1742 tarafından belirtilen gerekliliklere uygun olmalı ve aşağıdaki teknik gerekliliklere sahip olmalıdır:
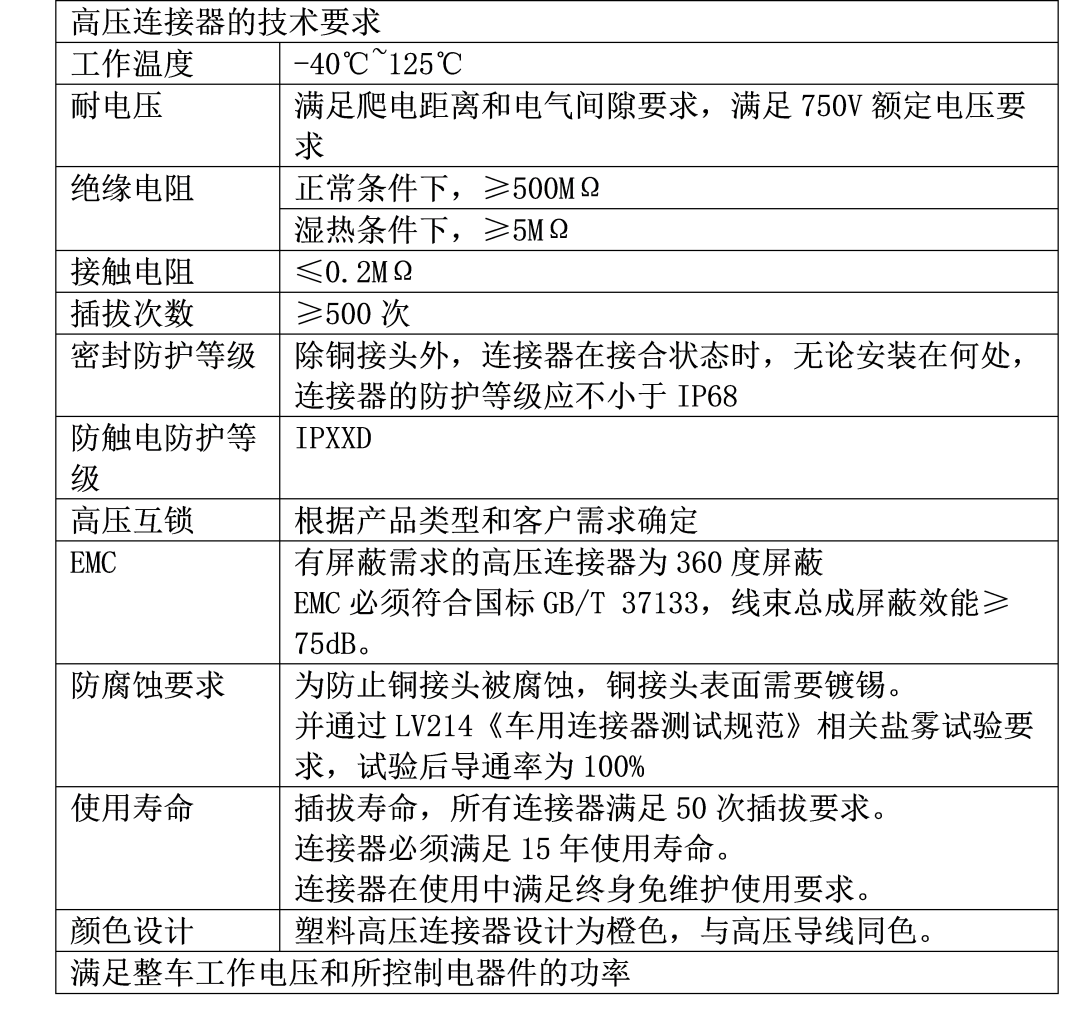
SAE J1742 tarafından belirtilen teknik gereksinimler
Yüksek gerilim konnektörlerinin tasarım öğeleri
Yüksek gerilim sistemlerinde yüksek gerilim konnektörlerine ilişkin gereksinimler şunları içerir ancak bunlarla sınırlı değildir: yüksek gerilim ve yüksek akım performansı; çeşitli çalışma koşullarında (yüksek sıcaklık, titreşim, çarpışma etkisi, toz ve su geçirmezlik vb.) daha yüksek koruma seviyelerine ulaşabilme ihtiyacı; monte edilebilirlik; iyi elektromanyetik koruma performansı; maliyetin mümkün olduğunca düşük ve dayanıklı olması.
Yukarıda belirtilen özellikler ve yüksek gerilim konnektörlerinin sahip olması gereken gereksinimler doğrultusunda, yüksek gerilim konnektörlerinin tasarımına başlarken aşağıdaki tasarım unsurlarının dikkate alınması ve hedeflenen tasarım ve test doğrulamasının yapılması gerekmektedir.
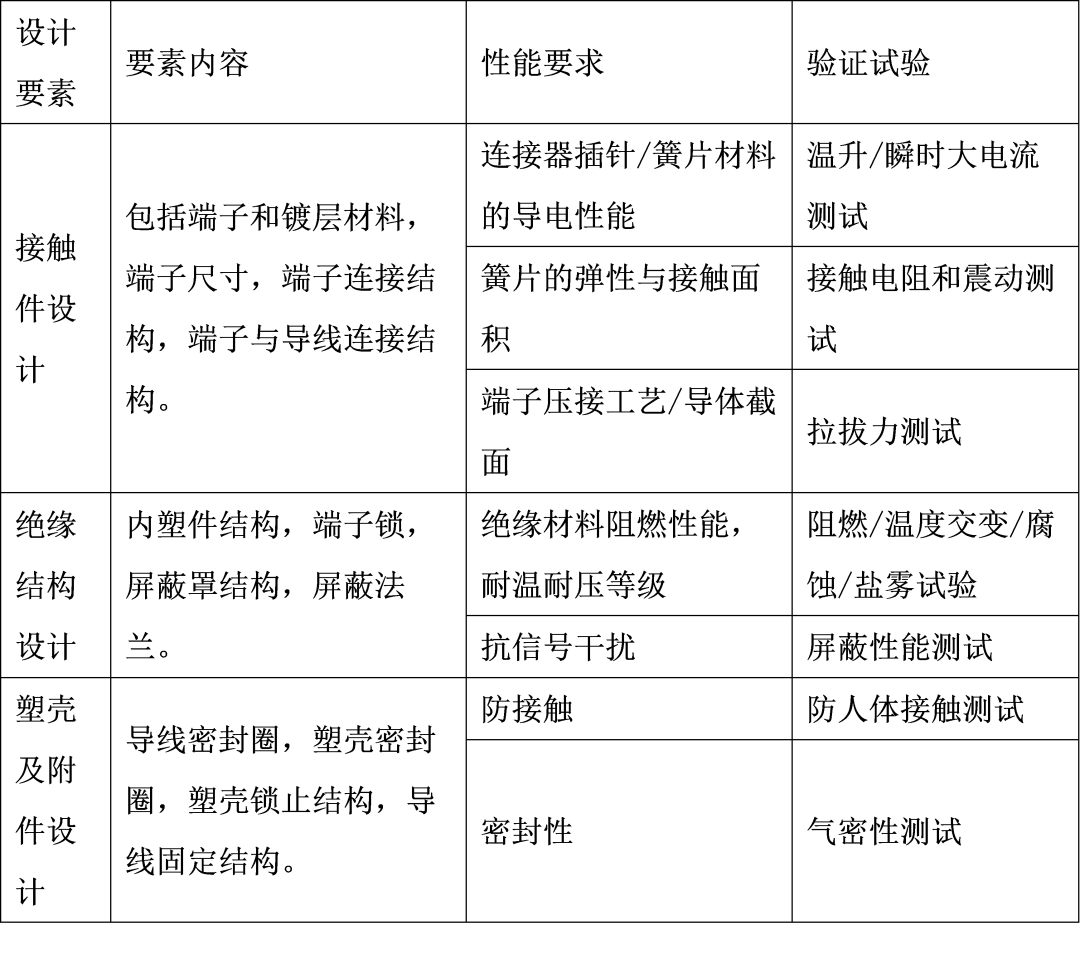
Yüksek gerilim konnektörlerinin tasarım öğelerinin karşılaştırma listesi, ilgili performans ve doğrulama testleri
Yüksek gerilim konnektörlerinin arıza analizi ve ilgili önlemler
Konnektör tasarımının güvenilirliğini artırmak için öncelikle arıza modunun analiz edilmesi ve buna uygun önleyici tasarım çalışmalarının yapılması gerekir.
Konnektörlerde genellikle üç ana arıza modu vardır: zayıf temas, zayıf yalıtım ve gevşek sabitleme.
(1) Zayıf temas için, statik temas direnci, dinamik temas direnci, tek delik ayırma kuvveti, bağlantı noktaları ve bileşenlerin titreşim direnci gibi göstergeler değerlendirmede kullanılabilir;
(2) Zayıf yalıtım için, izolatörün yalıtım direnci, izolatörün zaman bozulma oranı, izolatörün boyut göstergeleri, kontaklar ve diğer parçalar yargılanmak üzere tespit edilebilir;
(3) Sabit ve ayrı tipin güvenilirliği için, montaj toleransı, dayanıklılık momenti, bağlantı pimi tutma kuvveti, bağlantı pimi takma kuvveti, çevresel stres koşulları altında tutma kuvveti ve terminalin ve konektörün diğer göstergeleri test edilerek değerlendirilebilir.
Konnektörün temel arıza modları ve arıza biçimleri analiz edildikten sonra, konnektör tasarımının güvenilirliğini artırmak için aşağıdaki önlemler alınabilir:
(1) Uygun konektörü seçin.
Konnektör seçiminde yalnızca bağlı devrelerin türü ve sayısı değil, aynı zamanda ekipmanın yapısı da dikkate alınmalıdır. Örneğin, dairesel konnektörler dikdörtgen konnektörlere göre iklim ve mekanik faktörlerden daha az etkilenir, daha az mekanik aşınmaya maruz kalır ve kablo uçlarına güvenilir bir şekilde bağlanır, bu nedenle mümkün olduğunca dairesel konnektörler seçilmelidir.
(2) Bir konnektördeki kontak sayısı ne kadar fazlaysa, sistemin güvenilirliği o kadar düşük olur. Bu nedenle, alan ve ağırlık izin veriyorsa, daha az kontaklı bir konnektör seçmeye çalışın.
(3) Bir konnektör seçerken, ekipmanın çalışma koşulları dikkate alınmalıdır.
Bunun nedeni, konnektörün toplam yük akımı ve maksimum çalışma akımının genellikle çevredeki en yüksek sıcaklık koşullarında çalışırken izin verilen ısıya göre belirlenmesidir. Konnektörün çalışma sıcaklığını düşürmek için, konnektörün ısı dağılım koşullarının tam olarak dikkate alınması gerekir. Örneğin, güç kaynağını bağlamak için konnektörün merkezinden daha uzak kontaklar kullanılabilir; bu, ısı dağılımına daha elverişlidir.
(4) Su geçirmez ve korozyona dayanıklıdır.
Konnektör aşındırıcı gaz ve sıvıların bulunduğu bir ortamda çalışıyorsa, korozyonu önlemek için montaj sırasında yandan yatay olarak monte edilebileceğine dikkat edilmelidir. Koşullar dikey montaj gerektiriyorsa, sıvının iletkenler boyunca konnektöre akması önlenmelidir. Genellikle su geçirmez konnektörler kullanın.
Yüksek gerilim konnektör kontaklarının tasarımında önemli noktalar
Temas bağlantı teknolojisi, esas olarak terminaller ve teller arasındaki temas bağlantısı ve terminaller arasındaki temas bağlantısı da dahil olmak üzere temas alanını ve temas kuvvetini inceler.
Kontakların güvenilirliği, sistem güvenilirliğini belirlemede önemli bir faktördür ve aynı zamanda tüm yüksek gerilim kablolama tertibatının önemli bir parçasıdırBazı terminallerin, kabloların ve konnektörlerin zorlu çalışma ortamı nedeniyle, terminaller ile kablolar arasındaki bağlantı ve terminaller ile terminaller arasındaki bağlantı, korozyon, yaşlanma ve titreşimden dolayı gevşeme gibi çeşitli arızalara eğilimlidir.
Elektrik tesisatındaki tüm arızaların %50'sinden fazlasının hasar, gevşeklik, düşme ve kontakların kopması sonucu oluşan elektrik kablo demeti arızalarından kaynaklandığı göz önüne alındığında, aracın yüksek gerilim elektrik sisteminin güvenilirlik tasarımında kontakların güvenilirlik tasarımına da azami dikkat gösterilmelidir.
1. Terminal ve kablo arasındaki temas bağlantısı
Terminaller ve teller arasındaki bağlantı, ikisi arasında kıvırma veya ultrasonik kaynak işlemiyle yapılan bağlantıyı ifade eder. Günümüzde, kıvırma ve ultrasonik kaynak işlemleri, her birinin kendine özgü avantajları ve dezavantajları olan yüksek gerilim kablo demetlerinde yaygın olarak kullanılmaktadır.
(1) Kıvırma işlemi
Sıkma işleminin prensibi, iletken teli terminalin kıvrılmış kısmına fiziksel olarak sıkıştırmak için dış kuvvet kullanmaktır. Terminal sıkma işleminin yüksekliği, genişliği, kesit durumu ve çekme kuvveti, terminal sıkma kalitesini belirleyen temel unsurlardır.
Ancak, ince işlenmiş herhangi bir katı yüzeyin mikro yapısının her zaman pürüzlü ve düzensiz olduğu unutulmamalıdır. Terminaller ve teller kıvrıldıktan sonra, temas yüzeyinin tamamı değil, temas yüzeyine dağılmış bazı noktaların teması söz konusudur. Gerçek temas yüzeyi, teorik temas yüzeyinden daha küçük olmalıdır; bu da sıkma işleminin temas direncinin yüksek olmasının nedenidir.
Mekanik sıkma, basınç, sıkma yüksekliği vb. gibi sıkma işleminden büyük ölçüde etkilenir. Üretim kontrolü, sıkma yüksekliği ve profil analizi/metalografik analiz gibi yöntemlerle gerçekleştirilmelidir. Bu nedenle, sıkma işleminin sıkma tutarlılığı ortalama düzeydedir ve takım aşınması yüksektir. Etki büyüktür ve güvenilirlik ortalama düzeydedir.
Mekanik kıvırma yöntemi olgunlaşmış ve geniş bir pratik uygulama yelpazesine sahip geleneksel bir işlemdir. Neredeyse tüm büyük tedarikçilerin bu yöntemi kullanan kablo demeti ürünleri bulunmaktadır.
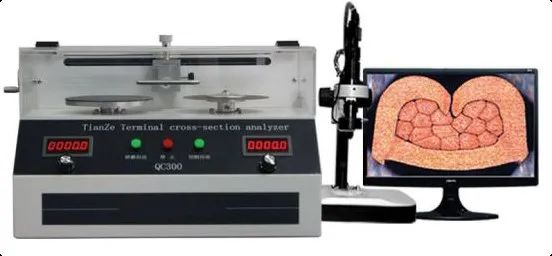
Sıkma işlemi kullanılarak terminal ve tel temas profilleri
(2) Ultrasonik kaynak işlemi
Ultrasonik kaynak, kaynak yapılacak iki nesnenin yüzeylerine yüksek frekanslı titreşim dalgaları iletir. Basınç altında, iki nesnenin yüzeyleri birbirine sürtünerek moleküler katmanlar arasında füzyon oluşturur.
Ultrasonik kaynak, 50/60 Hz akımı 15, 20, 30 veya 40 KHz elektrik enerjisine dönüştürmek için bir ultrasonik jeneratör kullanır. Dönüştürülen yüksek frekanslı elektrik enerjisi, dönüştürücü aracılığıyla aynı frekansta mekanik harekete dönüştürülür ve ardından mekanik hareket, genliği değiştirebilen bir dizi boynuz cihaz aracılığıyla kaynak kafasına iletilir. Kaynak kafası, alınan titreşim enerjisini kaynaklanacak iş parçasının birleşim noktasına iletir. Bu alanda, titreşim enerjisi sürtünme yoluyla ısı enerjisine dönüştürülerek metalin erimesi sağlanır.
Performans açısından, ultrasonik kaynak işlemi uzun süre küçük temas direncine ve düşük aşırı akım ısıtmasına sahiptir; güvenlik açısından, güvenilirdir ve uzun süreli titreşim altında gevşemesi ve düşmesi kolay değildir; farklı malzemeler arasında kaynak yapmak için kullanılabilir; yüzey oksidasyonundan veya kaplamadan etkilenir. Sonra; kaynak kalitesi, sıkıştırma işleminin ilgili dalga formlarını izleyerek değerlendirilebilir.
Ultrasonik kaynak işleminin ekipman maliyeti nispeten yüksek olmasına ve kaynak yapılacak metal parçaların çok kalın olmamasına (genellikle ≤5mm) rağmen, ultrasonik kaynak mekanik bir işlemdir ve tüm kaynak işlemi boyunca akım geçmez, bu nedenle Isı iletimi ve özdirenç sorunları, yüksek gerilimli kablo demeti kaynağının gelecekteki eğilimleridir.
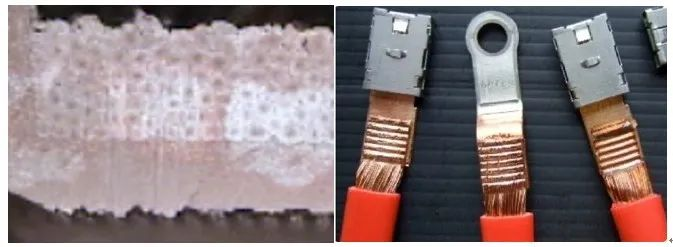
Ultrasonik kaynaklı terminaller ve iletkenler ve bunların temas kesitleri
Sıkma veya ultrasonik kaynak işlemi fark etmeksizin, terminal kabloya bağlandıktan sonra çekme kuvveti standart gereklilikleri karşılamalıdır. Kablo konnektöre bağlandıktan sonra çekme kuvveti, minimum çekme kuvvetinden az olmamalıdır.
Gönderi zamanı: 06-12-2023